Impact force and erosion tests are performed at our site.
The current nozzle as C nozzle and new nozzle as N nozzle were tested. The test method and evaluation are shown as follows. The test conditions went along with these conditions. -Pressure: 15MPa -Spray angle: 35 degrees Flow rate: 111L/min
Impact force test
The impact force test is a representative one in spray performance evaluation in an off-line site. The figure 1 shows a pattern diagram of the impact force test.
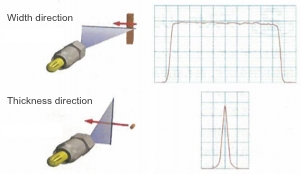
Impact force is measured by either method.
Spray nozzle with the requested flow rate and spray angle is selected and the impact force is measured, based on designated pressure.
The prototype is made and the impact force is measured by moving a load cell toward both spray width and thickness directions.
An uniform spray toward width direction is supposedly created.
The uniform impact force distribution and the impact force toward thickness are evaluated.
The most important thing is to increase the maximum impact force in this test.
The figure 2 shows the comparison example of C nozzle and N nozzle impact force data.

An uniformity of the impact force was maintained toward the width direction in two different models.
N nozzle was modified to gain 1.16 time more maximum impact force.
Recently, we are capable of conducting a three dimension impact force test, which enables us to gain more detailed information.
Erosion test
Scale removal on a steel surface with a descaling nozzle is considered to be mainly influenced by a water hammer phenomenon of water mass and water drop. Therefore, the erosion test is conducted by such as an aluminum plate (A5052A).
The figure 3 shows a schematic diagram of the erosion test.
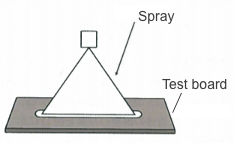
In the erosion test, an erosion amount is measured by spraying on the aluminum plate for a certain period time controlled by an automatic open and close shutter.
The figure 4 shows the test result
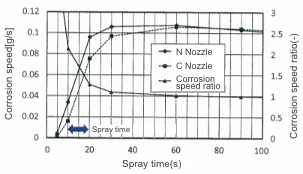
Along time going by, the erosion velocity on the aluminum plate increases,
and decreases after a certain time period.
The reason for the erosion velocity decrease is considered as the erosion
capability deterioration caused by a water pool.
After this kind of preliminary erosion test, we set up an appropriate evaluation time period, and start the erosion comparison test with same aluminum plate and spray time.