Descale nozzle is typically used at hot strip mill of steel company. Its flat fan pattern with high impact removes scale which is an oxidized layer on the surface of heated steel. This process is getting important in these years especially for producing steel for automotive as automotive manufacturers are chasing steel surface quality.
History
Nozzle tip used cemented carbide which is anti-wearing has been developed in 1957 as typical water pressure is more than 10MPa. This material is became usual idea for this kind of appreciation, and manufacturing method has been improved. When cemented carbide insert is manufactured, there are the procedure such as powder preparation, blending, forming, sintering and grinding.
On the other hand, a lot of improvement has been accumulated for nozzle structure also to have high descale efficiency. Filter has been developed in late 1960s, then built in straightener has been developed in late 1980. Making straighten flow has been investigated by each descale nozzle manufacturer as it is directly related with specification of descale nozzle.
Evaluation of scale removing
Off - line tests such as impact force measurement or erosion test by using aluminum plate were popular to evaluate descale nozzle. Because the evaluation method for descale nozzle by on - line test is not established.
Overview
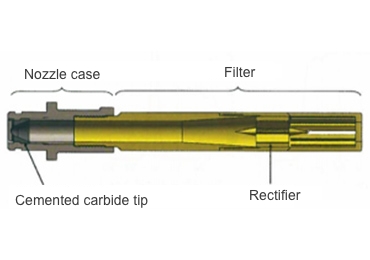
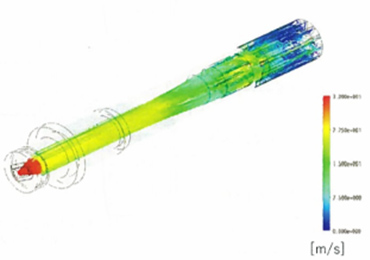
As Pic. 2 shows, cemented carbide insert is used as nozzle orifice where the fastest velocity to have anti - wearing. Although typical operation pressure is approximately 15MPa, it is getting higher to improve descale efficiency. We have different grades of cemented carbide which is harder than standard model for super high operating pressure.
Typical outer diameter of nozzle is 22mm. Also, 175mm overall standard length is the conclusion which we reached to after consideration of balance with internal flow pass. Typical flow rate/ spray angle are 40 - 200LPM/ 25 - 40 deg. Designing internal flow pass is one of the most important with fulfilling specification of customer's facility such as available pressure, flow rate of pump, space and nozzle layout.
We are developing nozzles by comparing actual result of spray test with simulation by improving analysis technology in these years.