Challenges
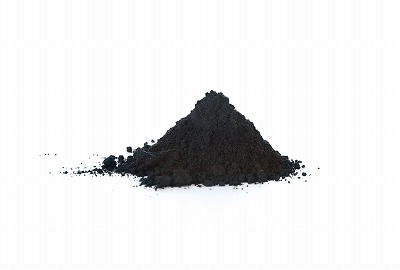
Carbon black is fine particles of carbon, produced by the incomplete combustion of oil. Typical applications include automobile and aircraft tires, belts, hoses, etc. It is also used as a black pigment in inks and paints, as well as for IT device touch panels.
One of the production methods for carbon black involves spray nozzles, however, since the raw material is sprayed under high pressure and high temperature, the nozzles are prone to wear. Worn nozzles cause changes in the flow rate and spray angle, leading to inconsistencies in particle size.
The customer previously used nozzles made by another manufacturer, however, was not satisfied with the proposals for improving wear resistance, so they contacted to us, a spray nozzle manufacturer with expertise in cemented carbide.
Solution
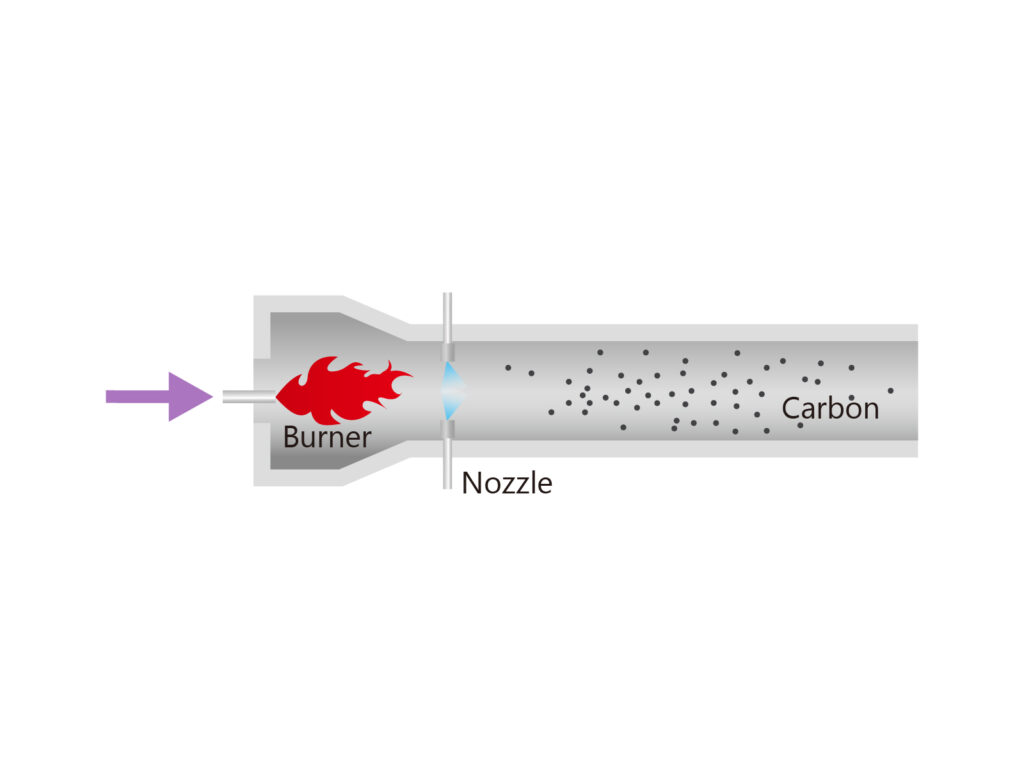
The conventional spray nozzles were made of stainless steel, however, we proposed replacing them with spray nozzles made from cemented carbide, which offers improved wear resistance and durability. Since the characteristics differ among cemented carbides, we selected several materials based on past results with similar pressure and temperature conditions and created prototypes.
Trail
First, we received the existing nozzle and performed analysis and evaluation tests on flow rate and spray angle to assess its performance. Since the customer was satisfied with the spraying performance, it was necessary to maintain performance while improving wear resistance and durability. We selected spray nozzles with similar performance and manufactured prototypes using cemented carbide materials (G2, G4). After prototyping, we repeatedly customized nozzle flow rate, spray angle, and other parameters to develop spray nozzles with greatly improved wear resistance and durability. In addition to in-house impact force testing to verify performance, we also conducted trials on actual equipment to confirm wear resistance. It was verified that wear resistance and durability had improved while maintaining performance, so we proceeded to mass production and supplied the nozzles to the customer.