Challenges
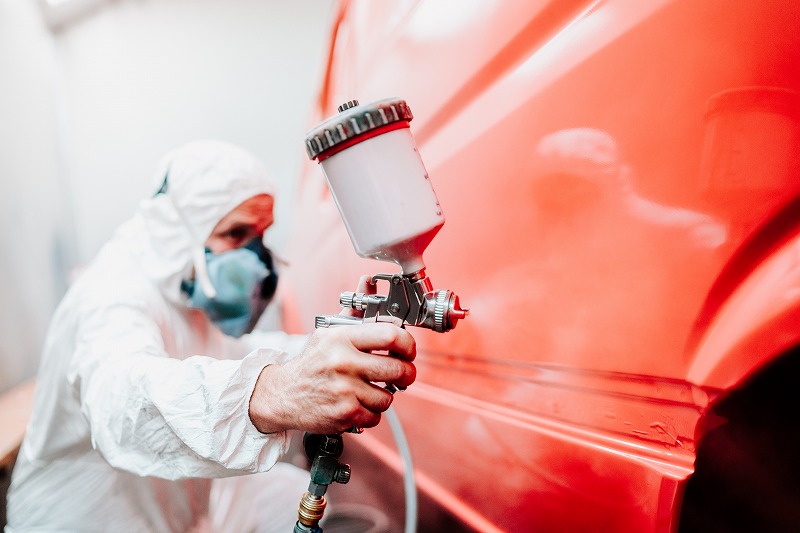
Spray nozzles are used in a process for high viscosity rust preventive coating on cars.
In this case, one of our customers requested a 360 degree uniform rust preventive spray at a low cost. In general, any even high viscosity liquid spray is not easy to control, and also a nozzle along the objects is required.
Additionally, 1,600 pieces of nozzles had to be delivered in 6 months. The design, the development, the prototype, the manufacturing and the delivery had to be completed within 6 months. The customer contacted us since their alternative suppliers were not able to meet the customer's requests including the delivery.
Solution
The current nozzle is an orifice type one. This type of nozzle costs more and its lead time is longer since the orifice type nozzle is embedded, which was a factor that their alternative suppliers was not able to meet the customer's requests. Figuring out that rust preventive coating was possible, based on our experiences for high viscosity spray such as seal material, we proposed a slit shape spray nozzle. Compared with the orifice type nozzle, the slit shape spray nozzle is more cost-effective and also its manufacturing lead time is shorter.
Trial
We evaluated the current nozzle with some water since the chemical liquid was not provided. Based on the flow rate from the evaluation, we selected the slit diameter. We made a prototype with a slit on different level on the circumference, and tested the spray. Our first prototype didn't provide an uniform distribution due to the nozzle internal pressure difference. Therefore, we made another prototype, changing the flow passage hole from 1 to 3.
This prototype created the uniform 360 degree spray. After our internal test, the prototype was installed in a customer's test equipment to coat some rust preventive. The test resulted in the uniformity even by some rust preventive. With the uniformity confirmation, we moved on the mass productions.