Challenges
Some exhaust gas is generated since massive amounts of garbage are burnt at garbage incineration facilities. The exhaust gas contains harmful substances such as sulfur oxide(Sox), nitrogen oxide(NOx), dioxin and others, which have to be properly treated. In general, a filtration type dust collector called bug filter is used. To let the exhaust gas flow through the bag filter, the gas temperature has to decrease down to less than 200 degrees Celsius to avoid activate the harmful substance such as dioxin. For this, cooling down is completed by spray nozzle's mist spray.
The sprayed water for gas cooling will be evaporated by mixing with some high temperature gas. However, the higher water ratio against the water gives rough particle sizes, which will cause some incomplete evaporation and end up creating some drain. The drain could cause the bag filter to be clogged. The bag filter is a post-stage equipment.
In this case, one of our customers was concerned that there would be any bag filter issues caused by some incomplete water evaporation. They would like us to avoid this kind of issue without any major existing equipment changes.
Solution
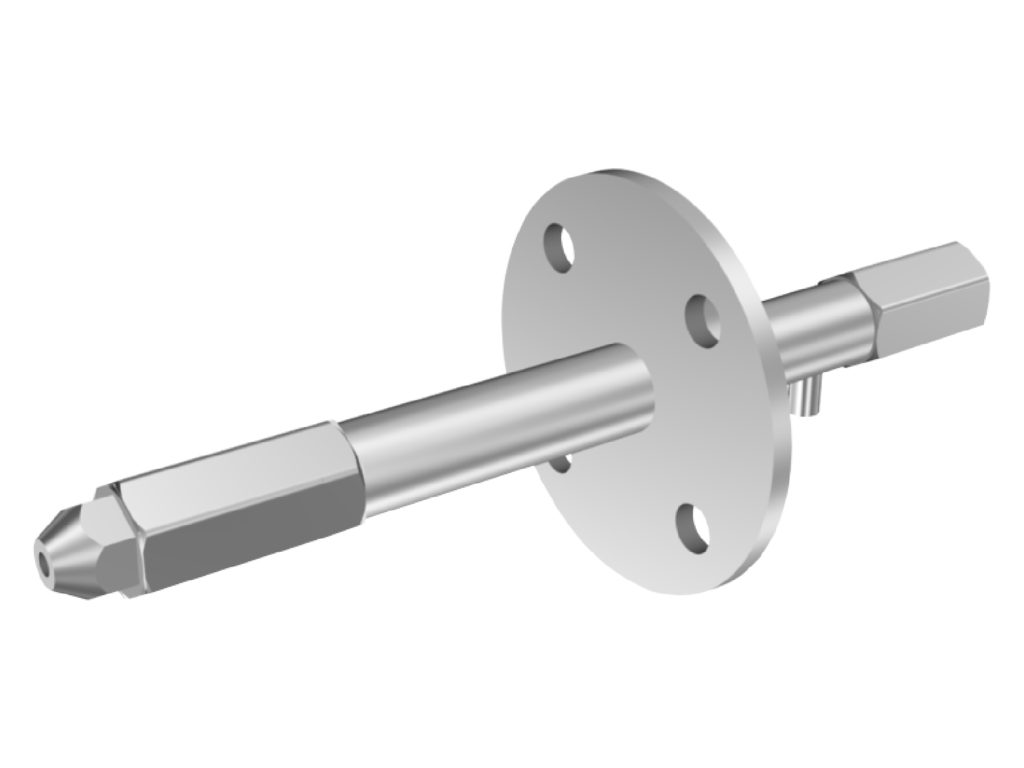
The reasons for the incomplete evaporation in the existing spray nozzles were as follows.
-Inefficient atomization
-The spray nozzle location
-The spray angle
A specialized spray nozzle was proposed since it was difficult to optimize air-to-water ratio and the spray angle with our standard spray nozzles. By optimizing these, without any major existing equipment changes, we thought that we would be able to solve the incomplete evaporation issue at a low cost.
Trial
Our specialized nozzle strength is to optimize atomization and spray angle. Checking the current nozzle spray angle and particle size, we analyzed ongoing issues.We proposed such a high atomization feature nozzle with an available air-water volume ratio by the existing equipment. We analyzed the optimal spray angel against the tower width and height, and designed a prototype. Repeatedly modifying the prot0ype, measuring the spray width, distance, particle size, we compared our nozzle performance with the existing one.
Going through some trials even on the customer equipment, we were able to confirm complete evaporation as the customer's requested. We were able to supply our nozzles meeting the customer's request.