Challenges
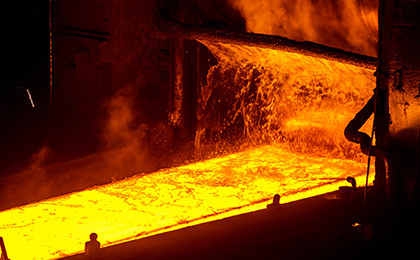
In the steel industry, continuous casting machines use mold cooling as primary cooling and spray nozzles for secondary cooling. During secondary cooling, the solidification of the slab occurs, so the uniformity of secondary cooling is a critical factor that significantly affects product quality.
Since hundreds of spray nozzles are installed on a single continuous casting machine, air consumption is extremely high. This results in increased compressor operation rates, leading to higher maintenance costs for compressors, increased electrical costs during compressor operation, and additional expenses associated with installing more compressors—all contributing to higher overall running costs. Reducing air pressure to limit air consumption would decrease spray performance, potentially causing surface cracks or deformation in the slabs, which would result in quality defects and could also damage production facility. Our customer in this case was looking for a spray nozzle that could reduce air consumption while maintaining cooling performance, without compromising spray quality.
Solution
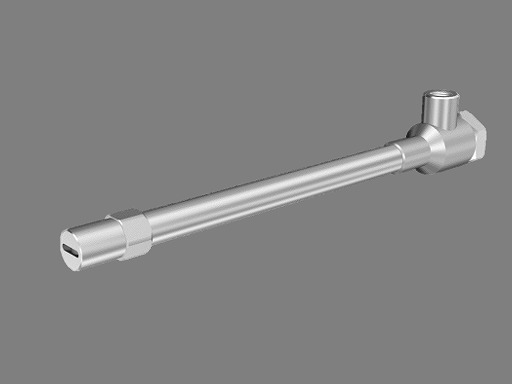
We collected the current spray nozzles and investigated their characteristics such as water distribution and air consumption. Based on our past experience, we then examined how much air consumption could be reduced while maintaining the same water distribution as the current nozzles, and presented our findings to the customer.
Trial
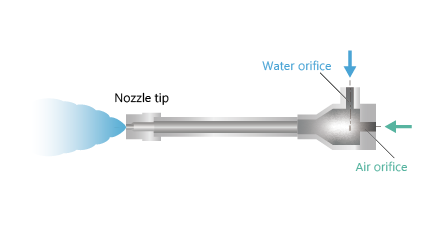
As mentioned above, we measured the water distribution of the conventional nozzles and investigated their characteristics, including air consumption.
Next, to reduce the amount of air required, we designed tailored nozzles by optimizing features such as the orifice shape of the nozzle tip—which affects distribution—as well as the air and water orifice that determine nozzle performance. Based on this design, we manufactured prototypes.
By repeating the process of measuring water distribution and evaluating cooling performance with Heat Transfer Coefficient(HTC) measurement system, followed by modifications and improvements to the prototypes, we succeeded in developing tailored nozzles that consumes less air than conventional nozzles while maintaining the same level of cooling performance.